Automatisierter Teiletransport bei Nobilia
vom 10. Oktober 2018
Beckhoff Automation: PC-based Control für bis zu 15 % effizientere Produktionslogistik.
Querförderwagen und Transportrollenbahnen von Horstkemper automatisieren Teiletransport bei Nobilia.
Nobilia, Europas größter Küchenhersteller mit Sitz in Verl, hat 2017 die immense Zahl von 675.000 individuell zusammengestellten Küchen ausgeliefert. Möglich ist dies nur mit einer intelligenten, hoch effizienten Produktionslogistik und durchgängiger Transparenz bei Teile- und Fertigungsdaten. PC-based Control von Beckhoff liefert hierfür die optimale Basis, wie es auch der mit Querförderwagen und Transportrollenbahnen von Horstkemper neu automatisierte Teiletransport im Produktionswerk II zeigt.
Nobilia setzt in seinen beiden Verler Produktionsstätten bei der Maschinen- und Produktionsautomatisierung schon seit 1989 durchgängig auf PC-based Control von Beckhoff. Dabei kann trotz des sehr heterogenen Maschinenparks mit homogenen, in der zentralen Nobilia-Datenbank vorgehaltenen Auftrags- und Teiledaten gearbeitet werden. Dies war der Schlüssel für eine über all die Jahre stetig verbesserte Effizienz und Flexibilität in der Produktion des Küchenherstellers sowie für die frühzeitige Umsetzung des Industrie-4.0-Gedankens.
Die große Zahl von rund 3.100 Küchen, die Nobilia im vergangenen Geschäftsjahr jeden Tag gefertigt hat, stellt entsprechend hohe Anforderungen an die Fertigungstechnik und -logistik. Um hier weiteres Wachstumspotenzial zu erschließen, wurde im 140.000 m2 Produktionsfläche umfassenden Werk II der Teiletransport mit Querförderwagen und Transportrollenbahnen der Horstkemper Maschinenbau GmbH, Rietberg, automatisiert. Dazu erläutert Geschäftsführer Norbert Horstkemper: „Wir bieten Nobilia individuell angepasste Logistiklösungen, wie in diesem Fall die Querförderwagen, für das Handling und den Transport von Küchenbauteilen an. Der Fokus liegt hierbei auf hoher Verfügbarkeit sowie kurzen Wartungs- und Installationsprozessen.“
Automatische Querförderwagen ersetzen manuelle Rollenwagen
Automatisiert wurde u. a. innerhalb der Teilefertigung ein am Auslauf mehrerer Bekantungsanlagen für Frontenmaterial liegender Transportbereich. Bislang wurden dort die fertig gestapelten Möbelteile mit manuellen Rollenwagen auf verschiedene Pufferbahnen sortiert, anschließend aus dem Pufferlager manuell an sogenannte Frontenkontrollplätze zur Säuberung und Prüfung der einzelnen Möbelteile verteilt und dann über ein nachstehendes Transportsystem ins Hochregallager transportiert.
Die technische Herausforderung bestand laut Norbert Horstkemper darin, die Transportabläufe so zu automatisieren, dass die Stapel mit Hilfe einer automatischen Zielvergabe in richtiger Reihenfolge und gleichmäßig sortiert über zwei Querförderwagen an ihre jeweiligen Ziele transportiert werden: „Zusätzlich sollte der automatisierte Frontenkontrollbereich für den Personen- und Staplerverkehr offen bleiben. Mit den Planungen für diese Aufgabe wurde Anfang 2017 begonnen. Die Umsetzung konnte nach dem Start im Mai bereits im Oktober beendet werden. Neben der Bedienerfreundlichkeit und Zuverlässigkeit der Anlage profitiert Nobilia von der schnellen Integration neuer Funktionen – teilweise während des laufenden Betriebs – in die bestehenden Systeme. Die Produktionsleistung hat trotz des Umbaus in kurzer Zeit wieder das normale Niveau erreicht und steigert sich seither weiter, da Nobilia kontinuierlich in die Automatisierung der einzelnen Transportbereiche investiert.“
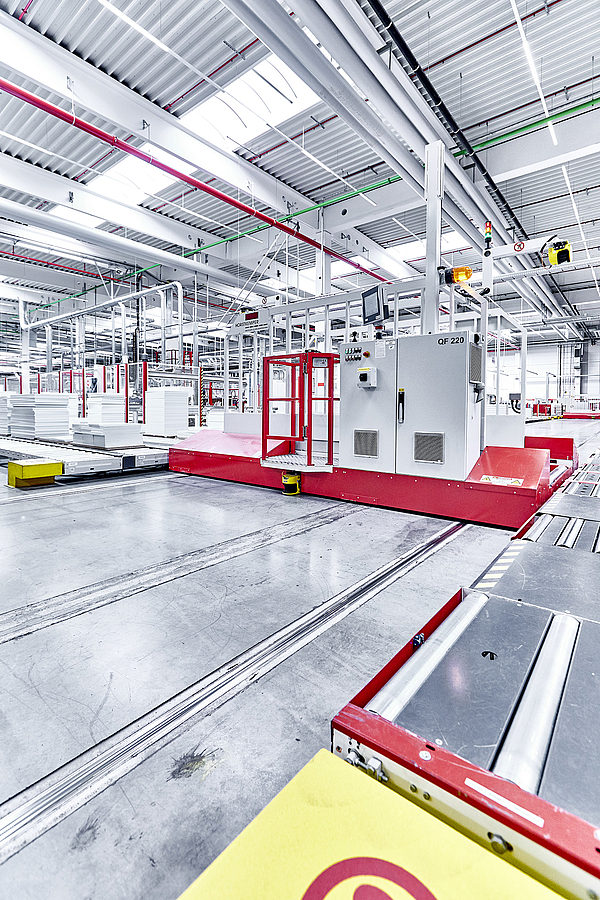
Die unterschiedlichen Querförderwagen können mit bis zu 85 m/min Geschwindigkeit verfahren, ohne den Personen- oder Staplerverkehr zu gefährden.
Deutliche Leistungssteigerung im Frontenkontrollbereich
Insgesamt zehn Querförderwagen automatisieren acht Transportbereiche mit rund 250 Transportrollenbahnen. Drei dieser Bereiche umfassen die Kontrolle und Nachbearbeitung der Möbelfronten. Dazu erläutert Lars Eberlei, Fertigungsplanung bei Nobilia: „Zusätzlich zu vorgeschalteten Inspektionssystemen werden die Frontplatten zu 100 % von den Mitarbeitern nachkontrolliert. Im Schichtbetrieb erreichen wir hier derzeit eine Ausbringungsmenge von fast 26.000 Teilen. Die Automatisierung mit Querförderwagen – mit vielen Materialein- und -ausgängen, Überschneidungsbereichen sowie Redundanzkonzepten – war ein großer Schritt, um die Teilestapel möglichst effizient zur richtigen Zeit an den passenden Ort zu transportieren. Gegenüber der vorherigen, bis auf einen großen Querförderer für schwere Schrankpakete rein manuellen Transportlogistik haben wir eine Leistungssteigerung von bis zu 15 % erreicht. Auf diese Weise konnte das Produktionswachstum mit dem gleichen Mitarbeiterstamm realisiert werden.“
Ein weiterer wichtiger Aspekt ist in diesem Zusammenhang laut Lars Eberlei die neue, auf den 24-Zoll-Multitouch-Control-Panels CP3924 von Beckhoff umgesetzte Visualisierung: „Ohne die realistische, mit Zoom-Funktion ausgestattete Darstellung des Transportbereichs mit allen Rollenbahnen und Querförderwagen wäre diese Effizienzsteigerung nicht möglich gewesen. Musste das Kontrollpersonal zuvor oft bis zu 14 km am Tag zurücklegen, um passendes Material zu finden, so kann nun einfach per Visualisierung die gewünschte Palette gesucht werden. Grundlage dafür ist das reibungslose Zusammenspiel dreier Komponenten: der Automatisierung durch PC-based Control, der Visualisierung und der für die gesamte Produktion zuständigen Warenleittechnik. Nur auf diese Weise konnten die Maschinen sowie der Transport- und der Kontrollbereich so eng und transparent zusammenwachsen, dass der Teilezugriff sich optimal steuern lässt und beispielsweise Stausituationen vermieden werden.“
Die Effizienzsteigerung durch die Warenleittechnik geht laut Lars Eberlei sogar weit über die zentrale Teileverfolgung hinaus: „Es wurde auch eine Abgabepriorisierung realisiert, um möglichst reibungslose Prozesse sicherzustellen. Außerdem wird die Mitarbeiterauslastung berücksichtigt. Danach erhält jeder Mitarbeiter für die Kontrolle nicht einfach nur das nächstverfügbare Teilepaket. Vielmehr wird zusätzlich auf eine regelmäßig abwechselnde körperliche Belastung durch unterschiedlich schwere Möbelteile geachtet. Weitere Funktionalitäten wie z. B. eine Restpalettenerkennung sind ebenfalls programmiert.“
Querförderwagen mit hoher Funktionalität und Sicherheit
Die Anzahl der verwalteten Querförderwagen variiert in den acht Transportbereichen zwischen 1 und 7. Die maximale Anzahl ist nicht begrenzt. Pro Transportbereich ist in der Regel ein Schaltschrank-PC C6930 vorgesehen. Der bereichsübergreifende Transport wurde so gelöst, dass die Bediener bei der manuellen Zielvergabe keine Einschränkungen in Kauf nehmen müssen. Die Anwahl von entfernt liegenden Transportzielen wird durch das automatische Routing über mehrere Transportbahnen und Transportbereiche ermöglicht. Bereits verlegte und zusätzliche Transportstrecken und Querförderwagen können über Parametertabellen jederzeit flexibel angepasst werden. Diese werden dann automatisch bei der Zielauswahl, der Transportlogistik und der visuellen Darstellung berücksichtigt.
Die Querförderwagen verfügen in der Regel über eine Traglast von 4 bis 5 t; in manchen Bereichen sind lediglich 2 t erforderlich. Um mit einem Transportvorgang möglichst viele Teilestapel zu transportieren, kann jeder Wagen vier bis sechs Stapel aufnehmen. Norbert Horstkemper ergänzt: „Die von den Platzverhältnissen bestimmte Breite der Querförderwagen liegt zwischen 2,50 und 4,50 m. Teilweise verfügen sie über mehrere Rollenbahnen, eine Hubeinheit und schützende Prallwände. Ein 19-Zoll-Multitouch-Panel-PC CP3219 mit TwinCAT NC PTP erledigt alle Steuerungsvorgänge, wie z. B. eine Breitenmessung und damit die Positionsbestimmung der Teilestapel auf der Tragrollenbahn. Für Motion Control kommen in Verbindung mit den AM8000-Servomotoren sowohl die kompakten EtherCAT-Servomotorklemmen EL72xx zum Einsatz – z. B. zur Steuerung der Prallwände – als auch die Servoverstärker AX5000 mit TwinSAFE-Karte AX5805. Über eine berührungslose Stromversorgung (IPT = Inductive Power Transfer) erhalten die Querförderwagen die nötige Energie. Ein ebenfalls berührungsloses, im Boden verlegtes absolutes Wegmesssystem trägt zusätzlich zu einem störungsfreien Betrieb bei. Die Datenanbindung an den zentralen Transportbereichsrechner erfolgt per WLAN. Von diesem Rechner erhält jeder Querförderwagen die Transportaufträge zum Aufnehmen und Abgeben des Materials.“
Erreichen lässt sich mit den Querförderwagen die hohe Verfahrgeschwindigkeit von maximal 85 m/min. Entsprechend wichtig ist die mit TwinSAFE systemintegrierte Sicherheitstechnik, da an zahlreichen Stellen der Fahrstrecken Personendurchgänge und Staplerverkehr zu beachten sind. Dazu erläutert Lars Eberlei: „Die Teiletransporte sind bei Nobilia zu rund 90 % automatisiert. Es gibt allerdings Nebenbereiche oder gesonderte Materialflüsse, wo dies nur sehr schwierig oder gar nicht möglich ist. Hier geben uns die Querförderwagen und PC-based Control die nötige Flexibilität, um solche Sonderprozesse reibungslos einzubinden.“
Komplexe Produktion durchgängig PC-basiert automatisiert
Allein der Transportbereich im Nobilia-Werk II ist mit ungefähr 1.500 Rollenbahnmotoren äußerst komplex. PC-based Control von Beckhoff bietet hier mit seiner Offenheit und Durchgängigkeit die optimale automatisierungstechnische Grundlage. Das modulare I/O-System der EtherCAT-Klemmen lässt sich genau auf die im jeweiligen Anlagenbereich gestellten Anforderungen abstimmen und außerdem bei Anlagenerweiterungen oder -modernisierungen einfach anpassen. Hinzu kommt die einheitliche Steuerung über TwinCAT, was u. a. das Zusammenlegen zuvor getrennter Anlagenbereiche – durch TwinSAFE auch in den sicherheitsrelevanten Segmenten – erleichtert. Weitere Vorteile ergibt die leistungsfähige Datenkommunikation. Das ultraschnelle EtherCAT ist u. a. für den sicheren Betrieb der Querförderwagen unerlässlich und die ADS-Kommunikation erleichtert die übergeordnete Kommunikation innerhalb der Produktion sowie die Anbindung an das Ethernet-basierte Firmennetzwerk von Nobilia. Dadurch lassen sich bestehende IT-Strukturen nutzen, um das Transportsystem beliebig und schnell erweitern zu können.
Norbert Horstkemper sieht neben der technischen Seite noch einen weiteren Vorteil von PC-based Control: „Die Zusammenarbeit zwischen uns als Maschinenbauer, Beckhoff als Steuerungslieferant und Nobilia als Endanwender hat inzwischen eine langjährige, erfolgreiche Geschichte. Das erleichtert zusammen mit der räumlichen Nähe vieles.“ Dies bestätigt auch Lars Eberlei: „Wir profitieren von der PC-basierten Steuerungstechnik ebenso wie von den direkt vor Ort verfügbaren Partnern. Dementsprechend wird PC-based Control auch in unseren Pflichtenheften gefordert.“
Die Flexibilität und gute Integrationsfähigkeit von PC-based Control zeigte sich bereits mit der beginnenden Automatisierung des Transportbereichs. So konnten die Kontrollarbeitsplätze zunächst im halbautomatischen Betrieb mit manuell vorgegebenen Transportzielen getestet und optimiert werden, sodass es zu keiner Produktionsunterbrechung kam. Dazu Lars Eberlei: „Die Automatisierung wurde problemlos und ohne Einschränkung der Produktionsabläufe umgesetzt. Hier hat neben der PC-basierten Technik auch die Erfahrung der langjährigen Partner eine große Rolle gespielt.“

An der Umsetzung der Transportautomatisierung beteiligt waren Christian Pankoke, Technische Dokumentation und Arbeitsvorbereitung bei Beckhoff Anlagentechnik, Arndt Tischler, Projektmanager Software bei Beckhoff, Lars Eberlei, Fertigungsplanung bei Nobilia, Norbert Horstkemper, Geschäftsführer von Horstkemper Maschinenbau, und Markus Laumeier, Projektleitung bei Beckhoff Anlagentechnik (v. l. n. r.)
Zukünftig weiteres Optimierungspotenzial erschließen
Das konsequente Weiterführen des Industrie-4.0-Gedankens eröffnet Nobilia zusätzliche Optimierungspotenziale. So soll mit der datentechnischen Anbindung von allen Maschinenstraßen und Handarbeitsplätzen möglichst weitgehend eine transparente Teileverfolgung und die automatische Zielvergabe realisiert werden. Durch das Mitprotokollieren wichtiger Transportparameter lässt sich der Auslastungsverlauf der einzelnen Querförderwagen und Transportrollenbahnen ermitteln. Diese Informationen können zukünftig als Grundlage bei der weiteren Optimierung der Transportstrukturen dienen. Lars Eberlei zieht folgendes Fazit: „Eine gut zu bedienende und schnell zu verstehende Applikation und ein entsprechendes HMI ist für die Zukunft und für neue Bediener unerlässlich.“
Quelle: Beckhoff PC Control - Ausgabe Nr. 3 - September 2018
Kontakt:
Horstkemper Maschinenbau GmbH
Helmut Wiesing
Löfkenfeld 65
33397 Rietberg-Mastholte
Tel.: +49 2944 / 9702 - 0
Fax: +49 2944 / 9702 - 33
E-Mail: h.wiesing@horstkemper.de
Internet: www.horstkemper.de